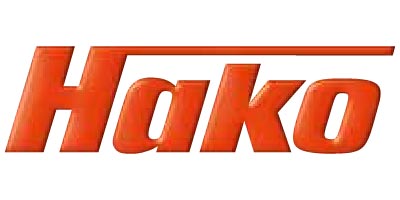
Hako zählt zu den weltweit führenden Lösungsanbietern für die Reinigungs-, Kommunal- und Wasserstrahltechnik. Mit einem großen Produktportfolio sowie umfassenden begleitenden Serviceleistungen bedient das Unternehmen mit Sitz in Bad Oldesloe eine breite Zielgruppe. Produktionswerke befinden sich in Deutschland, Polen und den USA.
viaLogs Projekte mit Hako
Zentralisierung der Logistik
Zentralisierung der Logistik
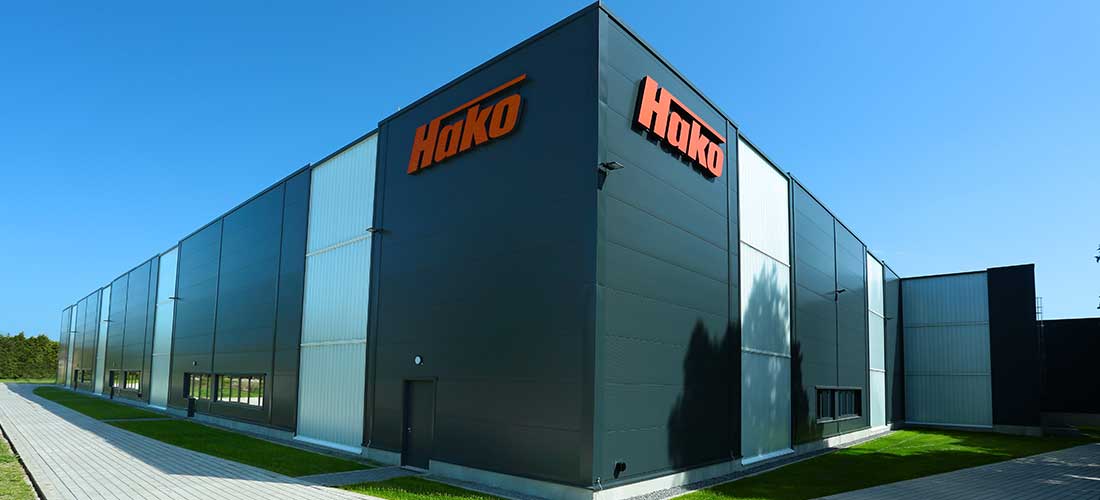
Die Herausforderung
Eine zergliederte Verkaufslogistik bei maximaler Auslastung und weiteres Wachstum als Ziel – für den Reinigungsmaschinen-Hersteller Hako war der Zeitpunkt für eine Neuaufstellung seiner Logistik erreicht.
„Durch stetiges Wachstum und den Ausbau unseres Produktportfolios lag unsere Flächenauslastung in den Werken zuletzt bei 100%, weiteres Wachstum ausgeschlossen“, begründet Joachim Blache, Geschäftsführer Operations bei Hako, die Entscheidung für den Neubau. „Gleichzeitig ließen sich die neuen Möglichkeiten digitalisierter Prozesse und Funktionen in den alten Strukturen nur unzureichend abbilden.“
Die Aufgabe
Neben der Unternehmenszentrale befinden sich am Standort im schleswig-holsteinischen Bad Oldesloe die Entwicklung, die Montage für Reinigungstechnik und ein Ersatzteillager. In einem etwa zwei Kilometer entfernten Gewerbegebiet unterhielt Hako noch bis Mitte 2023 ein Versandlager für Fertigerzeugnisse.
Der Neubau mit rund 14.000 qm Gesamtfläche schließt direkt an das Produktionsgebäude an und führt nun die Ersatzteil- und die Fertigwaren-Logistik unter einem Dach zusammen.
Die wichtigsten Zahlen im Überblick:
• > 40.000 vorrätige Ersatzteile
• 76.000 verfügbare Lagerplätze
• 7 LKW-Andockstellen
• 2.200 bearbeitete Positionen/Tag
• 500 versendete Pakete/Tag
„Durch die Zentralisierung der gesamten Prozesskette am Standort Bad Oldesloe erhoffen wir uns eine deutliche Verkürzung der Transportwege und -zeiten und letztlich eine noch höhere Servicequalität gegenüber unseren Kunden“, so Joachim Blache.
Fotos (3): Hako
Joachim Blache, Geschäftsführer Operations, Hako:
„viaLog hat uns mit einem Gesamtpaket aus konkreten Verbesserungsvorschlägen, projektspezifischem Know-how in den Bereichen Prozesse, Lagertechnik und IT, einem erfüllbaren und plausiblen Terminplan und Budget sowie einem positiven Eindruck in den Vorgesprächen überzeugt.“
Die Lösung
Hako beauftragte viaLog, die Konzeptplanung für das neue Logistik-Zentrum zu übernehmen. Nach dem erfolgreichen Abschluss der Planungsphase unterstützte das Berater-Team Hako bei der Detailplanung, Ausschreibung und Vergabe der Lagertechnik und Software. Zudem koordinierte viaLog als externes Projektmanagement die verschiedenen Gewerke während der Realisierung und Inbetriebnahme bis hin zum GoLive.
Insbesondere die sehr heterogene Artikelstruktur – von der großen Reinigungsmaschine bis hin zur einzelnen Schraube – verlangte eine gute Konzeptplanung. Im Ergebnis kommen unterschiedliche bedarfsgerechte Lagerformen zum Einsatz. Fertigerzeugnisse sowie großvolumige Ersatzteile und Zubehör werden zukünftig im Blocklager, in Breitgang- und Kragarmlagerregalen sowie in einer Verschieberegalanlage (ca. 6.500 Plätze) untergebracht. Kleinteile und Zubehör kommen in einer dreigeschossigen Fachbodenanlage (ca. 7.500 lfd. Meter) und einem AutoStore-System (19.500 Behälter) unter, das nach dem Ware-zu-Person-Prinzip arbeitet. Weitere Funktionsflächen strukturieren unter anderem die Wareneingangsbearbeitung, die Packerei inklusive Konsolidierung sowie die Versandbereitstellung.
LVS mit direkter Anbindung ans AutoStore
Damit alle Prozesse vom Wareneingang bis zum Warenausgang mit der neuen, modernen Einrichtungstechnik Schritt halten können, war die Einführung eines Lagerverwaltungssystems (LVS) für Hako ein weiterer folgerichtiger Baustein in der Planung. Das eingesetzte LVS verfügt über eine direkte Anbindung an das AutoStore und kommt ergänzend zur bisher genutzten ERP-Software zum Einsatz. Es soll für einen strukturierten Materialfluss über klare Funktionsbereiche sorgen und die Voraussetzungen für weiteres Wachstum schaffen.
Und auch in Sachen Mitarbeiterzufriedenheit sieht Joachim Blache Vorteile: „Das neue System ermöglicht uns unter anderem einheitliche Dialoge an allen Arbeitsplätzen. Die Abläufe werden insgesamt schneller, transparenter und weniger fehleranfällig, was auch unser Team zu schätzen weiß. Um unsere Mitarbeiter bestmöglich auf die neuen Prozesse vorzubereiten, wurden sie in die Projektphasen mit einbezogen und haben die Testphasen intensiv begleitet. Parallel wurden sie durch den LVS-Lieferanten geschult.“
Sukzessive Inbetriebnahme
Nach der termingerechten Fertigstellung des Logistikzentrums erfolgten die sukzessive Inbetriebnahme der Technik und der Umzug der Fertigwarenlogistik. Derzeit wird die neue Lagerverwaltungssoftware schrittweise hochgefahren. Der Umzug der Ersatzteillogistik ist ab dem 2. Quartal 2024 geplant.